Management column: Customized supply and delivery
September 5, 2023
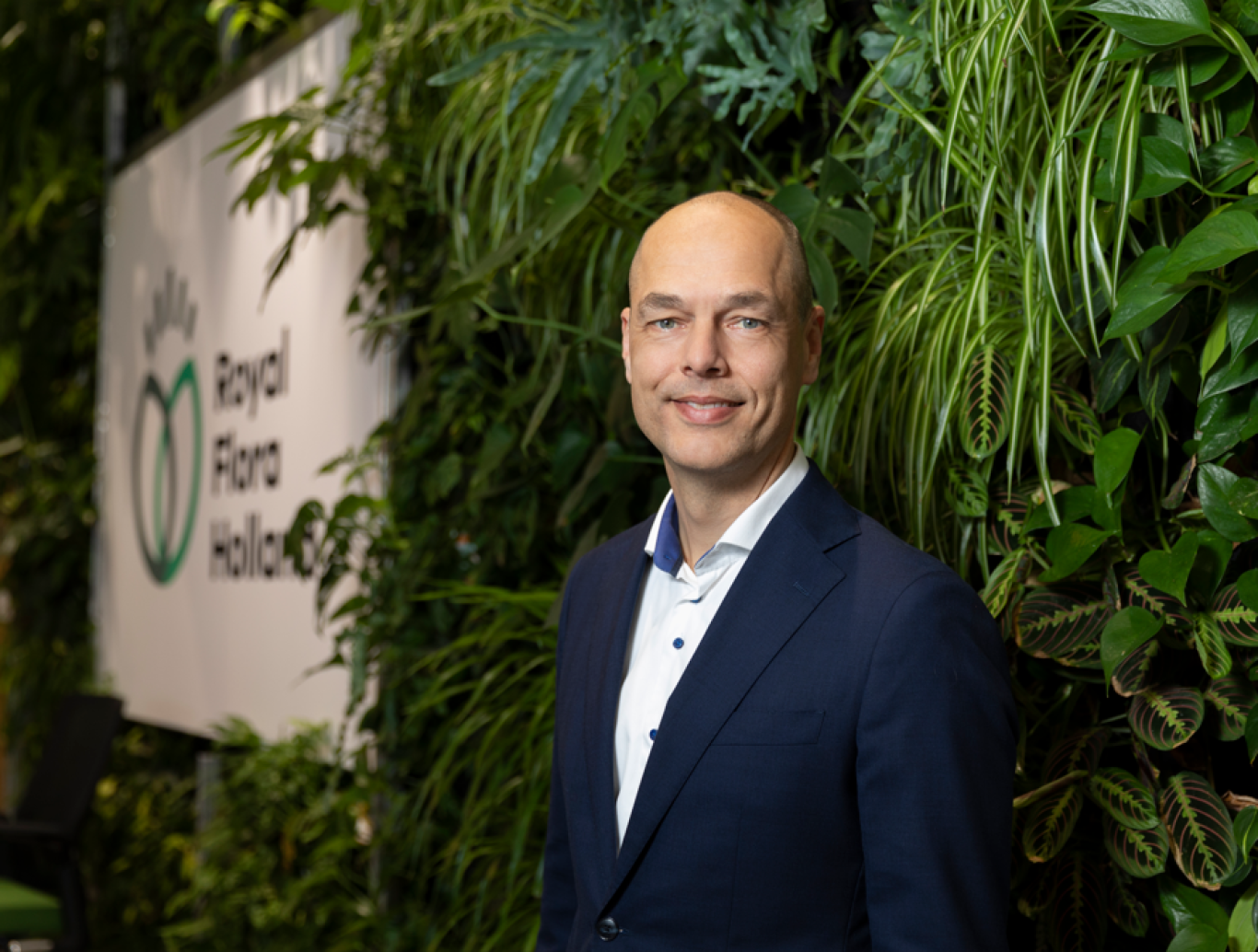
In this series of columns, we give the floor to Royal FloraHolland board members and managers: COO Leendert-Jan Plaisier about customized supply and delivery.
If anything is specific to floriculture, it is the huge diversity of growers and buyers. After all, no two companies are the same. Over the years, Royal FloraHolland's logistics services have, wherever possible, been the same for all customers. One-size-fits-all was simply the most efficient. In addition, the technological possibilities of doing things differently were lacking and IT systems still completely inadequate. This has undergone rapid change in recent times. What was previously unheard of is now a possibility. At the same time, we are also seeing growers and buyers adjusting their business operations. Shortages in the labour market, just like at Royal FloraHolland, are optimising the deployment of employees. The big challenge is to work together to make the chain as efficient as possible.
In spite of these shortages in the labour market, which are also putting pressure on our logistics operation, we decided last year to introduce order picking of flowers in Naaldwijk. This is a major step towards demand-driven logistics and standardisation of our processes and IT systems. As such, it presents numerous new opportunities in terms of supply and delivery today and into the future. We can back this up using what we have experienced in Eelde, Naaldwijk and Rijnsburg. Indeed, buyers visiting Aalsmeer are even asking if they can make the switch now! This shows that people recognise the opportunities. It is a proof to me and my team that we are on the right track and great motivation to persevere.
Part of our strategy is to set up our logistics to move with the logistical needs and requirements of growers and buyers. One example is the wishes of buyers to be able to decide on the delivery time themselves. Or growers' preference to combine products for Auction and direct during supply. This requires a shift in our logistics process. A warehouse management system based on order picking will allow us to turn this around: delivery needs are the guiding principle. In the near future, orders will be picked in the manner and at the time buyers want. Incidentally, in the case of Select Delivery, buyers already determine the delivery time for Auction Presales and will soon be able to do the same for their other purchases. Growers have the option of supplying their products to an RFH location and can subsequently offer fast delivery of direct orders from this stock and determine what proportion of products they supply through Auction.
We can further optimise the chain by processing Auction and direct in a single process. And this can be done with order picking. This also means: one method of supply and, eventually, even standardisation of stickering. We would really be making a lot of growers and buyers happy with this! In conjunction with Floriday and Floriway, opportunities are arising to optimise transport. For example, by managing and selling stock at our hubs from the nursery. Or by arranging direct inter-location transport at the push of a button when purchasing on the central auction clock, whereby products bought at one RFH location can be delivered to another location at a specified time.
By the way, I can well understand that not everyone is immediately responding to the promise of more options, more control over delivery times or pledges on convenience. After all, in terms of logistics, we certainly have a few things to prove. Another key focus is therefore reducing the number of errors. That’s because the quality of daily services remains priority number one. Although the development of service quality is a good thing, any error is obviously one too many. Which is why we are gradually changing so that growers and especially buyers can see how they can adjust their processes for a smooth turnaround. In the meantime, we are working towards enhanced expectations for order picking turnaround and delivery times. At the end of the day, all buyers should be able to count on a good forecast. In parallel, we are expanding time slots for Select Delivery. Depending on the wishes of the buyer, earlier or later delivery will again take pressure off the 'standard' process. This gives regular operations more breathing room; it also allows us to spread the work and means our employees can work more hours in a day. Buyers' experiences with Select Delivery have been very positive. I can sense from many that this tastes like more!
The next step is to switch completely to order picking in Naaldwijk, including for plants, with this move expected in the last few months of this year. This too, of course, is taking place gradually. Preparations are in full swing. And all experiences to date are being taken into account. Although we may have to just bite the proverbial bullet, as it were, I am convinced that all of us will come out of it all better off. That's what we're aiming for. Together with you.
If anything is specific to floriculture, it is the huge diversity of growers and buyers. After all, no two companies are the same. Over the years, Royal FloraHolland's logistics services have, wherever possible, been the same for all customers. One-size-fits-all was simply the most efficient. In addition, the technological possibilities of doing things differently were lacking and IT systems still completely inadequate. This has undergone rapid change in recent times. What was previously unheard of is now a possibility. At the same time, we are also seeing growers and buyers adjusting their business operations. Shortages in the labour market, just like at Royal FloraHolland, are optimising the deployment of employees. The big challenge is to work together to make the chain as efficient as possible.
In spite of these shortages in the labour market, which are also putting pressure on our logistics operation, we decided last year to introduce order picking of flowers in Naaldwijk. This is a major step towards demand-driven logistics and standardisation of our processes and IT systems. As such, it presents numerous new opportunities in terms of supply and delivery today and into the future. We can back this up using what we have experienced in Eelde, Naaldwijk and Rijnsburg. Indeed, buyers visiting Aalsmeer are even asking if they can make the switch now! This shows that people recognise the opportunities. It is a proof to me and my team that we are on the right track and great motivation to persevere.
Part of our strategy is to set up our logistics to move with the logistical needs and requirements of growers and buyers. One example is the wishes of buyers to be able to decide on the delivery time themselves. Or growers' preference to combine products for Auction and direct during supply. This requires a shift in our logistics process. A warehouse management system based on order picking will allow us to turn this around: delivery needs are the guiding principle. In the near future, orders will be picked in the manner and at the time buyers want. Incidentally, in the case of Select Delivery, buyers already determine the delivery time for Auction Presales and will soon be able to do the same for their other purchases. Growers have the option of supplying their products to an RFH location and can subsequently offer fast delivery of direct orders from this stock and determine what proportion of products they supply through Auction.
We can further optimise the chain by processing Auction and direct in a single process. And this can be done with order picking. This also means: one method of supply and, eventually, even standardisation of stickering. We would really be making a lot of growers and buyers happy with this! In conjunction with Floriday and Floriway, opportunities are arising to optimise transport. For example, by managing and selling stock at our hubs from the nursery. Or by arranging direct inter-location transport at the push of a button when purchasing on the central auction clock, whereby products bought at one RFH location can be delivered to another location at a specified time.
By the way, I can well understand that not everyone is immediately responding to the promise of more options, more control over delivery times or pledges on convenience. After all, in terms of logistics, we certainly have a few things to prove. Another key focus is therefore reducing the number of errors. That’s because the quality of daily services remains priority number one. Although the development of service quality is a good thing, any error is obviously one too many. Which is why we are gradually changing so that growers and especially buyers can see how they can adjust their processes for a smooth turnaround. In the meantime, we are working towards enhanced expectations for order picking turnaround and delivery times. At the end of the day, all buyers should be able to count on a good forecast. In parallel, we are expanding time slots for Select Delivery. Depending on the wishes of the buyer, earlier or later delivery will again take pressure off the 'standard' process. This gives regular operations more breathing room; it also allows us to spread the work and means our employees can work more hours in a day. Buyers' experiences with Select Delivery have been very positive. I can sense from many that this tastes like more!
The next step is to switch completely to order picking in Naaldwijk, including for plants, with this move expected in the last few months of this year. This too, of course, is taking place gradually. Preparations are in full swing. And all experiences to date are being taken into account. Although we may have to just bite the proverbial bullet, as it were, I am convinced that all of us will come out of it all better off. That's what we're aiming for. Together with you.
-
Did you find this interesting?
Then share this article