The innovative steps to efficiency in Dock Services
May 13, 2025
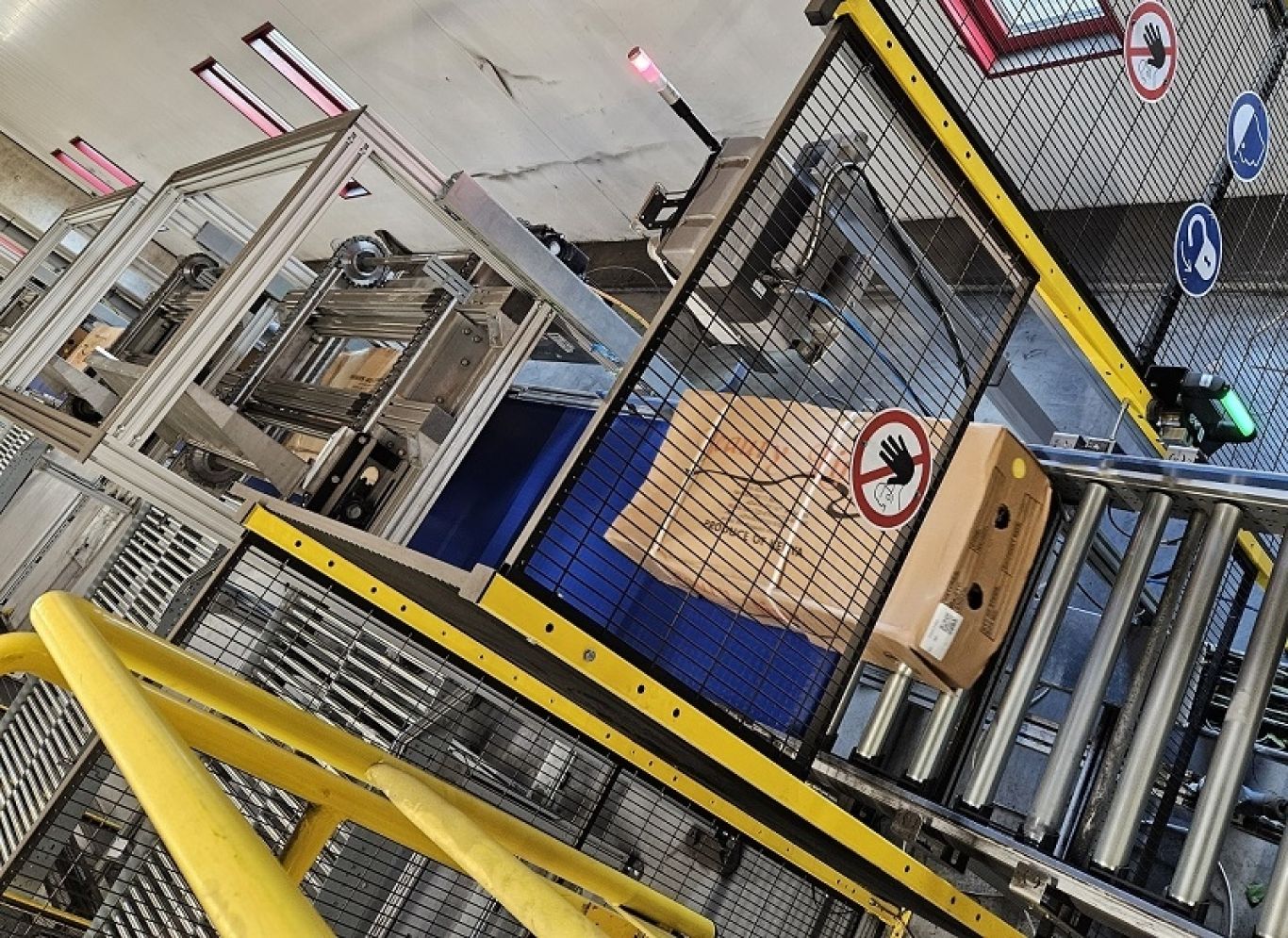
In early 2024, Dock Services took a big step forward. A 'smart' mechanical sorting system was installed to increase the throughput of flowers imported from Africa. After some initial challenges, much of the process is now fully automated and more efficient. Step by step, this leads to more and more benefits for customers.
Dock Services has been around for about 20 years. As part of Royal FloraHolland, it looks after 16 import agents representing around 50 growers at its three major logistics centres. "In Aalsmeer alone, the department handles around 4.6 million boxes a year," explains Bernard Piet, manager of Dock Services. "This means that we receive an average of 300 shipments of international floriculture products weekly. The flowers - mostly roses - come from Africa, the plants mainly from Italy."
The flowers are packed in boxes and brought to Dock Services from the airports of Liège, Brussels, Frankfurt, Maastricht and Schiphol. Importers can unload their products 24 hours a day. The team then sorts the incoming flowers and plants - by type, length, grower, buyer, order or any combination of these. The flowers are then delivered to the agent, who prepares the products for clock or direct sales. As an official inspection site, Dock Services also provides support for inspections by the Quality Control Bureau (KCB) and Customs.
Challenges
For many years, the sorting process at Dock Services Aalsmeer was manual, says Bernard. "But since last year, it has been done automatically. This means that flower boxes are now scanned and checked on the conveyor belt as they arrive. Throughput increases from 800 to 2,000 cartons per hour."
Such a move to automation has its challenges, says Bernard. "When making such changes, it is important that the whole chain is involved. Together, we form a network in which we need each other to achieve efficient processes. Once the new machine was in place, it took a few months for everything to fit together. For example, if not all growers pack and label correctly, this will cause delays. We regularly found that the information on the stickers on the boxes did not match the packing lists. Shipments were found to be incomplete. As a result, the sorting machine could not run at full speed, causing delays. Fortunately, all the teething problems are now behind us and our growers and agents know how important the label and correct information are.
Keep improving
Step by step, the improvements became noticeable and by the autumn of 2024, fortunately, before the peak period began, the fruits of this innovative investment could be seen. "The whole process is so much better now. The number of processing errors is reduced and products are processed faster. As a result, we can process more and more products.
In recent years, standards and communication in the chain have been greatly improved as a prerequisite for further mechanisation and efficiency. Bernard: "Just last year, boxes of hard-to-read instructions arrived from Africa. These boxes then contained all kinds of flowers of different lengths. Now they all have double stickers with QR codes on them, so everything is easy to track. This is a huge step forward and increases the efficiency of import processing."
Pro sport
The positive developments are reflected in the market. Recently, Marginpar began using Dock Services. Meanwhile, Bernard and his team continue to focus on further process improvements. "Our profession is sometimes like pro sport," says Bernard. "You are as good as your last game. So we have to make sure we keep improving."
Dock Services has been around for about 20 years. As part of Royal FloraHolland, it looks after 16 import agents representing around 50 growers at its three major logistics centres. "In Aalsmeer alone, the department handles around 4.6 million boxes a year," explains Bernard Piet, manager of Dock Services. "This means that we receive an average of 300 shipments of international floriculture products weekly. The flowers - mostly roses - come from Africa, the plants mainly from Italy."
The flowers are packed in boxes and brought to Dock Services from the airports of Liège, Brussels, Frankfurt, Maastricht and Schiphol. Importers can unload their products 24 hours a day. The team then sorts the incoming flowers and plants - by type, length, grower, buyer, order or any combination of these. The flowers are then delivered to the agent, who prepares the products for clock or direct sales. As an official inspection site, Dock Services also provides support for inspections by the Quality Control Bureau (KCB) and Customs.
Challenges
For many years, the sorting process at Dock Services Aalsmeer was manual, says Bernard. "But since last year, it has been done automatically. This means that flower boxes are now scanned and checked on the conveyor belt as they arrive. Throughput increases from 800 to 2,000 cartons per hour."
Such a move to automation has its challenges, says Bernard. "When making such changes, it is important that the whole chain is involved. Together, we form a network in which we need each other to achieve efficient processes. Once the new machine was in place, it took a few months for everything to fit together. For example, if not all growers pack and label correctly, this will cause delays. We regularly found that the information on the stickers on the boxes did not match the packing lists. Shipments were found to be incomplete. As a result, the sorting machine could not run at full speed, causing delays. Fortunately, all the teething problems are now behind us and our growers and agents know how important the label and correct information are.
Keep improving
Step by step, the improvements became noticeable and by the autumn of 2024, fortunately, before the peak period began, the fruits of this innovative investment could be seen. "The whole process is so much better now. The number of processing errors is reduced and products are processed faster. As a result, we can process more and more products.
In recent years, standards and communication in the chain have been greatly improved as a prerequisite for further mechanisation and efficiency. Bernard: "Just last year, boxes of hard-to-read instructions arrived from Africa. These boxes then contained all kinds of flowers of different lengths. Now they all have double stickers with QR codes on them, so everything is easy to track. This is a huge step forward and increases the efficiency of import processing."
Pro sport
The positive developments are reflected in the market. Recently, Marginpar began using Dock Services. Meanwhile, Bernard and his team continue to focus on further process improvements. "Our profession is sometimes like pro sport," says Bernard. "You are as good as your last game. So we have to make sure we keep improving."
-
Did you find this interesting?
Then share this article